職場改善をしたいが何をしていいか分からない期間工へ
期間工は本当に真面目な人が多いと思っています。みんな同じ方向を向けば本当に力強いですし、能力が高い方も多いように感じています。
このブログでも非常に多くの現役の方、恐らくは期間工も正社員も含めての事だと思いますが、閲覧してくださっています。本当にありがたい事です。
さて、このブログの訪問者を分析するにあたって、皆さんがお困りなのは創意くふうや改善提案のようです。
これはトヨタ自動車での創意くふう提案をもとに作った記事ですが、どうもトヨタだけではなく、デンソーやホンダや日産の方もヒントを求めに来てくださっているようで、重ね重ねありがたくブログ冥利に尽きます。
創意くふうや改善提案の見つけ方、私が思うにこれは「見つける癖」の問題だと思っていまして、訓練というか、考え続けていたらネタは浮かんでくるものだと思っています。
そこで今回、上に紹介した記事を少し補足する意味でも、創意くふうや改善提案を見つけやすくする考え方についてまとめてみようと思います。
改善箇所を見つけるために必要な意識
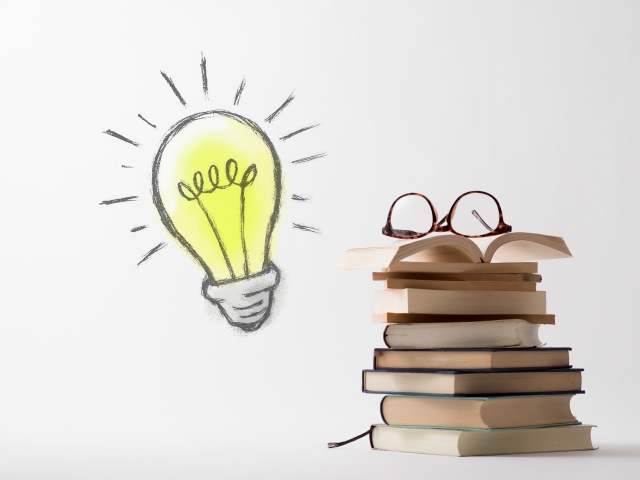
創意くふうを月間3枚や5枚、新入社員は10枚書き上げなければならない。そんなノルマを課せられたのに、どうにも見つからない、なかなか改善箇所がない。
そういうときにまず癖にしてもらいたいのは、「改善できる場所は無いか」という事をずっと考え続けるという意識を持つことです。
ずっと、というのは文字通り「ずっと」です。工場の門をくぐってから、工程で働く間ずっとです。
理想をもってすべてを見ていく癖を持つ
創意くふうや改善は、1つの視点を持つことで見つけやすくなります。
「この場所で完璧な状態は一体どんな状態だろう?」という視点です。
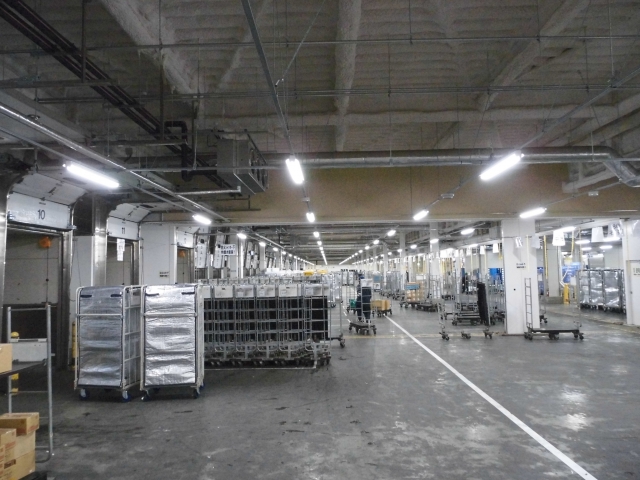
例えばこの工場の写真を見て、理想的な状態はどんな状態なのだろうと考えるわけです。実際働いてみなければ事情は分かりませんが、もしかすると、映っているカートが全くない状況が理想かもしれません。少なくとも、右にも左にも台車があるのは理想とは思えませんよね。
同じようにして自分の現場でも、理想の状況、改善できそうなところはどこだろう?と考えます。
表示がされていない。
区画が決められていない。
区画からはみ出している。
歩行帯がない。
床面が濡れている。
実際の工場の中でも似たような事はあると思います。
「なんだヒヤリハットか、単純な事ばっかりじゃないか」と思う方もいると思いますが、実際の工場を見るとこういう単純な事もなかなか完璧に実行されていないんです。
これをずっと考えておくだけです。
棚が1つあったら、ちゃんと定物定置が徹底されているのか、定量は守られているのか、その表示はあるのか。棚が2つあったら、棚を1つにできないのか、置き場所は分かりやすいのか。
そのためには、理想になる状態を知っておかなければいけません。でもそのお手本になる場所は工場のそこかしこに転がっているので、それを横展していくだけです。
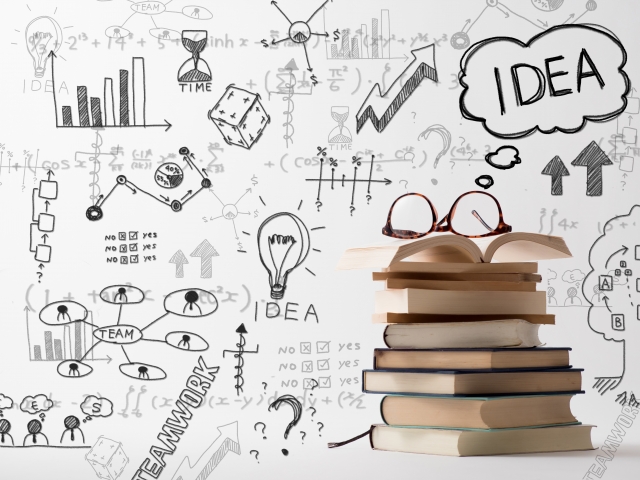
ECRSの業務改善方法
ECRSは改善点の英語の頭文字です。生産性を向上させるために作られたものがECRSという方法があります。
E・・・無くせないか
C・・・一緒にできないか
R・・・順番を変えられないか
S・・・単純にできないか
という視点です。最初に、その対象となる作業や工程を無くせないか考え、次にその作業の前後や工程の前後を一緒にできないか考え、やり方を見直し、単純かを図れないか、という順番に見ていくというものです。
ずっとそのことを考えておかなければアイディアは浮かばないですし、理想の状態を知らなければ同じく改善しようがありません。
もっと分かりやすい言葉で考える
ECRSが分かりづらい場合は次の言葉を問いかけてみるといいと思います。
「もっと簡単にできないか」
「もっと早くできないか」
「もっと安全にできないか」
「もっと削減できないか」
「もっと綺麗にできないか」
「もっと分かりやすくできないか」
このテーマをもって見ていく事で、改善が必要な場所が見つけやすくなります。
例えば今自分がやっている作業、もっと簡単にやる方法は無いか考えます。
工具をセットする場所、ワークの向き、取り回し、台車の位置、メンテナンスなどもそうです。
もちろん細かな変更でも上長の許可が必要なケースもあるので勝手にやる事はできないので、出来そうな部分があれば相談をもちかけてみることが最初です。
取りづらい部品があれば取りやすくする方法は無いだろうか。
棚に置いている備品は手前を取れば奥から次が出てくるスライド式にすれば補充が簡単になります。
例えばピッキング
ピッキングの最も理想の状況というと、バーコードスキャンすれば全部自動で出てくる、というものです。完全自動化です。
それが難しいので、バーコードスキャンすればピッキングしなければならない棚の指定の箇所がランプ点灯し、ピック出来ればランプを消す、というものでしょうか。
それも難しければ車種ごとにピッキングルートを床に貼り、個数と品番が書かれたボードをチェックしながら追っていく。
色分けをしてみる。タグ付けをする。重量測定をする。表示を変えてみる。
理想の状態からどんどん妥協をしていくほど取り組みやすくなります。現実に近づくからです。Aパターン、Bパターン、Cパターン、手段や方法をあれこれ想像していく。1つにこだわらず、実現可能か不可能かは一度置いておいて、こうしたらやれるかも?を探していく事をずっと続けるのです。
最終的には、そもそもピッキング作業を無くすにはどうすれば良いか、というのを考えることがその工程の最大の課題でしょう。
定位 定品 定量 定路 定色
5定や5Tと呼ばれるもので、整理整頓に関する考え方です。
定められたものが、定められた場所に、定められた量だけ置かれているか。経路は決まっているか。色分けされているか。またそれらの表示がきちんとできているかも重要です。
こうした定め方が徹底されているかどうかも、改善にはかなり効果的な見方になります。提案書にも「5Tに従って」と書きやすくなるのでおすすめの見つけ方です。
メモに5Tを書いておくと、思い出しやすくなります。
王道は、やりづらい作業を探すこと
トヨタで言うところの5WHY分析法、これは訓練が必要で、単純なようで結構難しい方法です。
慣れていないとどうしても3回目や4回目のWHYでループしてしまうので、質問者にかなり左右されてしまいます。
そこで使いやすいテクニック、というより視点は、これも王道ですが、やりづらい作業をひたすら考えて見ることです。
後ろを向いて工具を取り、前を向いて作業するのがやりづらいなら、工具を前に持ってくることを考えるほうが良いですよね。
ネジをとるのがやりづらいなら、ネジを個数分だけ下から受ける方法を採用すべきですし、実際そうしている工程はすでにあるので横展してもらえば良いですね。
床にカスが落ちて作業途中に4Sが入るなら、下にごみ箱を置いておけないか考えたほうが早いです。
1枚ずつ取りづらいなら弱い粘着式のテープで取り上げられるかもしれません。手袋の材質の問題かもしれません。
やりづらい作業を改善できれば作業時間も短縮できますから、そうした点もアピールできれば高額案件になりやすいのです。
ムリ・ムラ・ムダを探せとはよく言われますが、こうした部分を考え続けることで創意くふうや改善提案は常にストックを持つ事ができるようになります。
最初にお伝えしたように、これは一つの癖です。考え続ける癖を持つだけで、どんどん見えてくるようになる癖です。
今日一日これだけ考えてみてください
今日一日、区画と表示がちゃんとされているかだけ考えてみてください。そこだけに注目してみていけば、きっと未着手の場所が残っているはずです。
ラック置き場は全部区画線が設定され、その通りに置かれているか。
歩行帯はちゃんと設定されているか。
棚の区画は完璧か。
ドアに注意の表示はあるか。
棚には正しい表示があるか。
ラックの上の置き場は定物定置になっているか。
電気スイッチはどこが付くか表示はあるか。
壁のフックは何を掛けるか表示されているか。
台車は持ち手部分がグリーンテープで決められているか。
工場は常に変化するから改善が追いつかないのが当たり前
特にトヨタ自動車の工場はレイアウトが頻繁に変わりますよね。レイアウトが変わるという事は、それに伴って台車の場所、備品棚の場所、区画、コンセントの位置や配線も変わるという事です。
こうした大きな変化がいつもどこかであるわけですから、歩行帯の修正や区画の再設定、台車置き場や備品の並びもどんどん変わっていきます。
新しい工具や棚が増えることも珍しくありませんし、ごっそり無くなる事も珍しくありませんよね。
だからこそ表示関係は改善が追いつかないのが当たり前なので、単価は低いですがそうした修正が創意くふうや改善提案で可能になってくる。
ただ機械やその周辺については表示は法律・法令に関わる部分もあるので、特に大型機械の周辺の創意くふうや改善は上長の確認をとるようにしましょう。
そういえば、詰め所の棚の表示、意外とできてないところ多いんですよね。誰もやらない事をやるところに意味があったりしますからね。
理想的な状況を知るためのちょっとした取り組み
動画にも出てきますが、工場の中の「からくり技術」を知るのはアイディアをもらえるのでおすすめです。
またこれと同様に、別の工場動画を見て、工場内の表示や仕組み、理想像を探すのは横展開できる引き出しになります。完全自動化された工場や安全対策動画などもそうです。
ピッキングでミスをなくすにはAmazonの動画やユニクロの動画が参考になります。現在の産業の最先端をどうやって取り入れるかは結構重要な事だと思います。
平日勤務なのでかなり厳しいとは思いますが、機会があれば他社の工場見学に行くのもおすすめです。ワイン工場やビール工場、明太子工場、陶磁器製造工場、せんべい工場などもありますが、それぞれの業界でそれぞれの取り組みがあるので、横展できる事がいくつも見つかります。
改善の箇所を見つけるのは考える癖付けが大事、それだけでも覚えて帰っていただければ幸いです。
ディスカッション
コメント一覧
まだ、コメントがありません